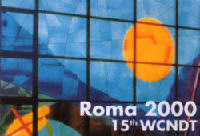 | Human Reliability in Ultrasonic Inspection
Alexiev Al., M. Mihovski |
1. IntroductionNon-destructive testing (NDT) is one of the most successfully used inspection methods in the nuclear and thermal electrical plants. The various factors have effect to the reliability of the ultrasonic NDT as well as the working practising, the long working hours, the local environment, inherent capability of the inspectors (training, qualification, experience), applied inspection systems and procedures etc. Some national and international programmes have been accomplished, including PISC programme[1-7]. The first local programme for radiation NDT in Bulgaria was realised in 1985 [8]. During 1999 the new investigations of ultrasonic NDT of welded joints were organised. The aim of this paper is to present the organisation and the test results obtained in 1999. The factors investigated include: the accuracy of coordinates and of amplitudes from artificial reflectors determinations and the quality of acoustic coupling during ultrasonic inspection. 2. Organisation of the inspection reliability studies2.1 Participants All persons (2 groups of 16 and 18 participants) which within the last 15 years were members of the NDT groups, working either as UT inspectors, have participated in the tests. All persons were holders of UT certificates level II, according to the BDS EN 473. The participants in the test groups actually have performed UT professionally. The working conditions was: temperature - 25° C, humidity - 50%, noise level - 45dB A.2.2 Examiners Two persons participated in the test with UT certificates level III, according to the BDS EN 473. They have a perfect knowledge of the equipment usage and posses considerable experience in welded joint inspection and examine of inspectors. 2.3 Equipment The following equipment had to be available in order to perform the tests: Sigma 1000 is a training device for education and examination of NDT personal for ultrasonic inspection of welded joints and working with standard ultrasonic device. Sigma 1000 provides simulation of butt welds with thickness from 10 to 150 mm made of Fe, Al, Ti or Cu, using angle transducers of 35°, 45°, 60° or 70°. The length of the weld is 400 mm and of the heat-affected zone is 250 mm. The simulation of discontinuities is acquired by the placement of piezoelectric reflectors under the heat-affected area. The electronic system permits different reflector types to be used to provide the appearance of real discontinuities together with false signals (indications). An automatic record of results is foreseen of true and falls replies. Additionally the amplitude of the signals are included [9 - 11]. The system covers simulation of hundreds variants of welded joints. ISONIC is an intelligent ultrasonic test system for manual testing. The system consist of four components: personal computer with additional control electronics and application programs, air - borne sound location system, coupling monitoring system and digital ultrasonic flaw detector (in this case USK7D). For the aim of our investigation of planar welded joints the major features of the ISONIC system software is the documentation of scanning pattern, top view, side view, all calibration data of the system, coupling sensitivity, colour location, according to amplitude height and evaluation of the results (amplitude (between +12dB to -12dB) and distance from discontinuities measurement). The coupling monitoring system consist of a noise generator which is coupled to any point of the test object. The amplitude of received from frequency noise signal allows the evaluation of the coupling quality. The coupling results quality and the results of discontinuities are presented in real time during scanning. A plate test specimen with thickness 20mm from aluminium alloys was prepared for the test. Seven blind reflectors have been elaborated in the part, simulating a welded joint: R1 - side cylindrical reflector with diameter 2,7mm and depth 24mm; R2 - R5 - flat bottom cylindrical reflectors with diameter 2,7mm and depth 7 mm; R6 - flat bottom cylindrical, oriented in the direction of the ultrasonic beam with diameter 2,7mm and depth 24 mm; R7 - a groove with sizes 36x0.5x1 mm. The roughness of the heat - affected area is Rz=10-15 μm. 2.4 Working programme The programme for investigation the reliability of the inspectors, working manually under typical on-site conditions compared to their performance under laboratory conditions includes: Introduction to the Sigma 1000 and ISONIC systems. Preparation of the procedures according to the Bulgarian standards for ultrasonic test of welded joints on the base of information available about the materials, thicknesses, welding processes, possibilities of the ultrasonic device USK7D. Examination with Sigma1000 and USK7D. The operator determinates the coordinates of the reflectors registered (X - along the specimen length, Y - from the centre of the transducer to the centre of welded joint, Z - the acoustic path from the centre of the transducer to the reflector) and the echo amplitude. Upon detection of a reflector, the operator confirms it by pressing a specified button. Examination with ISONIC During the test the operator works with USK7D only in accordance to the procedure elaborated by him. The ISONIC system is connected to USK7D and is tuning up by examiner. The latest is the only one who has access to it. At the end of the test ISONIC issues a protocol of the inspection. A typical protocol are represented at Fig.1 and Fig.2 for two NDT operators with different rate of the acoustic coupling. The appearance of all reflectors (R1 to R7) are presented at Fig.1. In the upper area, the presence of darkening corresponds to an acoustic coupling better then the given by examiners one. The results obtained have been statistically elaborated by the examiners. The characteristics determinated by the test with ISONIC, are: total area of darkening with coupling guaranteed; the area of indications - STV in the Top View and SSV in the Side View; the maximal amplitude registered for each reflector Ai. 3. Experimental results3.1 Experimental results from Sigma 10000 The measured values for ferric steel plate with thickness 30 mm are displayed in Fig. 3 - Fig. 6 for 3 reflectors (R1 - R3). In the Table 1 the generalised input records are shown from the test of the group inspectors.Table 1 N | 1 | 2 | 3 | 4 | 5 | 6 | 7 | 8 | 9 | 10 | 11 | 12 | 13 | 14 | 15 | 16 | A | 3 | 2 | 2 | 3 | 3 | 2 | 3 | 3 | 2 | 2 | 2 | 2 | 3 | 3 | 2 | 2 | B | 0 | 1 | 1 | 0 | 0 | 1 | 0 | 0 | 1 | 1 | 1 | 1 | 0 | 0 | 1 | 1 | C | - | 1 | 3 | - | - | 3 | - | - | 3 | 3 | 2 | 1 | - | - | 3 | 3 | D | 0 | 1 | 1 | 0 | 0 | 1 | 0 | 0 | 1 | 3 | 1 | 1 | 0 | 0 | 1 | 0 | T | 30 | 25 | 15 | 25 | 10 | 35 | 15 | 25 | 15 | 20 | 30 | 25 | 25 | 20 | 25 | 25 | N is a number of the participant of the test, A - the number of properly detected reflectors, B - the number of non - detected reflectors, C - the sequential number of the of non - detected reflector, T - the test duration in minutes. 43% of the examined operators have found out all the reflectors without registration of false echoes. The worst are the results obtained on R3 reflector. One participant has registered 3 false echoes. The duration of the inspection is from 10 to 35 min. On the base of the test results, the participants have been divided into 3 groups: I (7 participants) with best results, II (8 participants) with average results, and III (1 participant - N10) with 3 false echoes registered. Using the methods presented in [12, 13], the average values and the uncertainty u for A, X, Y and Z have been calculated for reflectors R1 - R3 (Table 2). The uncertainty is determined for level of confidence 0,95, were u=2s (s - standard deviation). In the accounts are taken into consideration only the results of those participants, who have registered the relevant discontinuities. Table2 |  | uA, dB | , mm | uX, dB | , dB | uY, dB | , dB | uZ, dB | R1 | 78,9 | 14,49 | 180,7 | 4,92 | 45,1 | 5,42 | 70,9 | 5,21 | R2 | 77,5 | 16,30 | 268 | 5,84 | 24,7 | 8,08 | 45,1 | 6,55 | R3 | 79,2 | 7,99 | 299,3 | 3,11 | 30,2 | 8,80 | 43,9 | 4,42 | 3.2 Experimental results from ISONIC. Fig.7 to Fig.10 present the main data obtained from the experiments performed with a group of 18 participants, after the evaluation of test reports by the examiners. Fig.7 show the area S, which the inspectors are scanning with good acoustic coupling. The area of heat-affected zone, which must be scanning is S0=2,73•104 mm2. A good coupling has been achieved in more then 70% of the heat - affected zone, where the ultrasonic transducer moves. In this case the uncertainty us=3,71•103 mm2. In Table 3 the test results are generalised using the same symbols as in Table 1. Table 3 N | 1 | 2 | 3 | 4 | 5 | 6 | 7 | 8 | 9 | 10 | 11 | 12 | 13 | 14 | 15 | 16 | 17 | 18 | A | 4 | 7 | 7 | 7 | 7 | 7 | 4 | 6 | 6 | 6 | 7 | 6 | 5 | 6 | 6 | 7 | 7 | 7 | B | 3 | 0 | 0 | 0 | 0 | 0 | 3 | 1 | 1 | 1 | 0 | 1 | 2 | 1 | 1 | 0 | 0 | 0 | C | 2,5,6 | - | - | - | - | - | 2,5,6 | 6 | 5 | 1 | - | 5 | 2,5 | 1 | 1 | - | - | - | T | 20 | 25 | 10 | 25 | 10 | 10 | 15 | 15 | 20 | 10 | 10 | 20 | 15 | 15 | 25 | 25 | 10 | 20 | 50% of the participants have discovered all 7 reflectors, 33% - 6 reflectors, 11% - 4 reflectors. The operators tested have difficulties with R2, R3 and R6. The duration of the inspection was from 10 to 35 min. The average values of STV, SSV and A and there uncertainties have been determinated using the methods from [12, 13] (Table 4). Table 4 | R1 | R2 | R3 | R4 | R5 | R6 | R7 |  | 126,6 | 45,1 | 85,5 | 82,5 | 49,4 | 49,3 | 211,3 |  | 108,46 | 47,96 | 70,58 | 70,38 | 41,55 | 47,22 | 181,57 | | 107,6 | 55,9 | 66,6 | 63,6 | 50,5 | 38,6 | 165,5 | | 125,35 | 50,75 | 90,75 | 46,81 | 49,10 | 52,02 | 147,24 | | 63,7 | 62 | 63,5 | 65,5 | 66,5 | 62,3 | 70 | uA, dB | 6,17 | 8,26 | 6,96 | 6,21 | 9,43 | 7,57 | 7,45 | 4. ConclusionsThe reliability test performed, allows to make the following conclusions: A small number of inspectors sometimes give seriously wrong results due to the human factor. This can be corrected by supplementary training and multiple inspection. The majority of the inspectors is doing their inspection with satisfying uncertainty during tests with ISONIC. The environmental conditions of the test performed with ISONIC are very favourable. Therefore, in reality the deviations of inspectors results is expected to be larger then the reported values. The devices Sigma 1000 and ISONIC are convenient for training and examinations of inspectors. In 2000 such tests will be included in the education and training curriculum of the high education centre "KVALIMA" in Bulgaria.
The authors thank to the companies Sonotron Ltd. (Israel), G.Shoef Ltd. (Israel), NDT - products and systems (Bulgaria) and The Bulgarian Ministry of Education and Science (Project TN819) for the support. 5. References- Mletzko Ul.: Results of Mini round Robin on the Reliability of Ultrasonic Testing. Proceeding of First International Conference on NPE in Relation to Structural Integrity for Nuclear and Pressured Components. 20 - 22.10.1998, Amsterdam Woodhead Publishing Limited, Cambridge, England, V. I, p. 124.
- Spanner I., D. Harris: Human Factor Developments in Computer Based Training and Personnel Certification, Proceeding of First International Conference on NPE in Relation to Structural Integrity for Nuclear and Pressured Components. 20 - 22.10.1998, Amsterdam Woodhead Publishing Limited, Cambridge, England, V. I, p. 149.
- McGrath B. A.: Programme for the Assessment of NDT in Industry, AEA Technology
- Human Reliability in Inspection, Final Report on Action 7 in the PISC III. Programme, Report N 31, Commission of the EC, Joint Research Centre, Ispasite, 1999
- Waites C., G. M. Worral: Improving the Reliability of On-side NDT Inspection OECD/NEA - IAEA Symposium on Human Factors and Organisation in NPP Maintenance Outages Impact on Safety, Stockholm, 1995.
- Worral G.: Human Factor in Relation to Inspections Carried Out at NPP, AEA Technology, 1998, Slide serial N 2.
- Murgafroyd R. A., G. M. Worral, S. Crutzrn: Lesson Learned from the PISC III Study of the Influence of Human Factors on Inspection Reliability, 6th European Conference on NDT, 1994, Nice, 989-993.
- Mihovski M., M. Lozev: Nondestructive testing in chemical machine building, Technica, Sofia, 1987
- Passi G.: High-reliability manual ultrasonic testing, Defectoscopija, 12, 1998, 49-65
- Toebben P., W.-D. Kleinert, M. Berke: ISONIC - Complete Ultrasonic Weld Inspection Documentation by Continuous Recording of Manual Probe Manipulations, Acoustic Coupling and Echoes, 7-th ECNDT, Copenhagen, 1998, 3032 - 3039.
- Gurvich A., G. Passi: Comparison of nonautomated systems for the acoustic nondestructive testing of welded joints, Defectoskpija, 1991, 2, 3 - 9.
- EAL "The expression of the uncertainty in quantitative testing", EAL - G23, 1, 1996.
- EAL "The expression of the uncertainty of measurement in calibration", EAL - R2, 1, 1997.
|