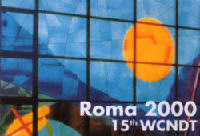 | Ultrasonic Inspection and Mapping of Internal Glass Coating in Reservoirs and Reactors
A.Golden, V.Moshkovich, A.Passi, G.Passi, R.Safin, Sonotron NDT - Israel |
A great number of pipes, reactors and reservoirs are in use in chemical industry worldwide for processing, storing and transportation of different aggressive materials.In many cases, the metallic wall is protected with internal glass coatings. To ensure the safety of aging equipment the glass coating must be inspected periodically. A new technique was created to implement ultrasonic inspection of glass coating while scanning from outside with true-to-scale mapping of test integrity and defects. The technique based on real time spectrum analysis of echo received from "metal to glass" border and mechanics free probe location through the use of airborne ultrasound. As a result, a three-color map is obtained in real time while scanning above metal surface: 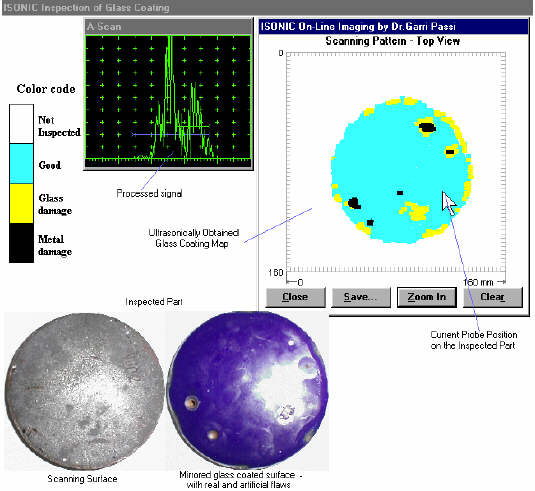 The Map shows: - actually inspected non-damaged area ("no defect" color)
- defects, which are classified in real time automatically in two categories:
- pitting in the glass without penetration into the metal (imaged with "glass damage" color)
- pitting in the glass with penetration into the metal (imaged with "critical defect - metal damage" color)
The described technique is commercialized as the GLASSMAP software package for the rugged portable battery operated ISONIC workstation and uses the standard set of ISONIC accessories for mechanics free monitoring of the ultrasonic probe coordinates and acoustic coupling. The appropriate ultrasonic probe must be used to implement glass coating inspection, for example DA 312 or MSEB 5 from Krautkramer or similar. Inspection results are stored on disk and then plotted as glass coating map. Postprocessing also features: - automatic measurements of defect coordinates
- sizing defects
- creating comprehensive defects list
|